ISO 9001 is an international standard for quality management systems (QMS) developed by the International Organization for Standardization (ISO). It offers a comprehensive framework and guidelines that organizations can use to implement effective quality management practices, ensuring they consistently meet customer expectations.
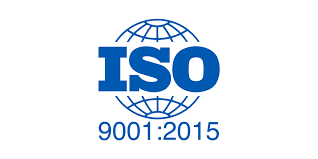
Key Principles of ISO 9001
The ISO 9001 standard is built on several core principles:
- Customer Focus: Prioritizing customer satisfaction by understanding and meeting their needs.
- Leadership: Establishing a strong leadership structure that drives commitment to quality.
- Engagement of People: Involving all employees in quality management processes.
- Process Approach: Managing activities as interrelated processes to ensure consistency.
- Improvement: Continuously improving processes to enhance performance.
- Evidence-Based Decision Making: Basing decisions on data analysis.
- Relationship Management: Building and maintaining strong relationships with stakeholders.
These principles help organizations develop a systematic approach to quality management, improve customer satisfaction, and drive continuous improvement.
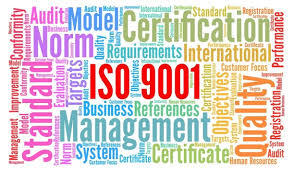
ISO 9001 Certification
Organizations that adopt ISO 9001 demonstrate a commitment to delivering high-quality products or services, improving customer satisfaction, and achieving operational excellence. To obtain ISO 9001 certification, organizations must meet several key requirements:
- Context of the Organization: Understanding the internal and external factors that impact the organization, including the needs and expectations of stakeholders.
- Leadership: Establishing clear direction, demonstrating commitment to quality, and fostering a customer-focused culture.
- Planning: Setting quality objectives, conducting risk assessments, and developing plans to achieve these goals.
- Support: Providing the necessary resources, infrastructure, and training to support the QMS.
- Operation: Implementing processes that meet customer requirements and managing product or service delivery effectively.
- Performance Evaluation: Monitoring performance indicators, conducting audits, and analyzing data to assess the QMS’s effectiveness.
- Improvement: Continuously improving the QMS by addressing nonconformities and enhancing processes.
ISO 9001 certification, though not mandatory, offers numerous benefits, including increased credibility, access to new markets, and enhanced customer trust. Certification is granted after a successful audit by an accredited certification body.
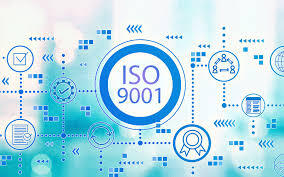
The Importance of ISO 9001
ISO 9001 is crucial for organizations across various industries for several reasons:
- Customer Satisfaction: By focusing on customer needs and consistently delivering high-quality products or services, ISO 9001 helps organizations improve customer satisfaction, leading to repeat business and positive referrals.
- Quality Management: ISO 9001 provides a structured framework for establishing effective QMS, which enhances operational efficiency, reduces errors, and improves resource management.
- Continual Improvement: The standard promotes a culture of ongoing improvement, encouraging organizations to identify areas for enhancement and implement changes systematically.
- Legal and Regulatory Compliance: ISO 9001 helps organizations comply with relevant laws and regulations, reducing risks and maintaining a strong reputation.
- Market Access and Competitive Advantage: ISO 9001 certification can open new market opportunities and give organizations a competitive edge by demonstrating their commitment to quality.
- Organizational Efficiency and Effectiveness: By standardizing processes, organizations can improve efficiency, reduce waste, and enhance overall effectiveness.
- Employee Engagement and Empowerment: ISO 9001 encourages the involvement of employees in quality management, leading to higher morale and productivity.
ISO 9001 and Maintenance Work Orders
While ISO 9001 does not specifically address maintenance work orders, its principles can be applied to maintenance processes within an organization:
- Process Approach: Organizations can define clear procedures for handling work orders, ensuring consistency and standardization.
- Customer Focus: Internal customers, such as equipment operators, benefit from timely and effective maintenance work orders, enhancing satisfaction.
- Planning and Control: ISO 9001 encourages effective planning and control, which can be applied to prioritize tasks, allocate resources, and monitor progress in maintenance work orders.
- Continual Improvement: Regularly evaluating work order processes and implementing corrective actions can lead to more efficient maintenance management.
- Documentation and Record-Keeping: Properly documenting work orders ensures traceability and supports decision-making for future maintenance activities.
- Auditing and Monitoring: Regular audits of work order processes help ensure compliance and continuous improvement.
Benefits of Maintenance Software with ISO 9001
Integrating maintenance software with ISO 9001 can significantly enhance the effectiveness of a QMS:
- Document Control: Centralized storage and management of documents ensure easy access and version control, supporting compliance with ISO 9001.
- Process Standardization: Maintenance software enforces standardized workflows and procedures, promoting consistency and adherence to ISO 9001 requirements.
- Work Order Management: Streamlined work order processes ensure tasks are documented, tracked, and completed efficiently.
- Equipment and Asset Management: Maintenance software helps maintain accurate records of equipment, supporting compliance with asset control and calibration requirements.
- Data Analysis and Reporting: Software-generated reports provide insights into maintenance performance, supporting data-driven decision-making.
- Audit and Compliance Management: Maintenance software assists in scheduling audits, tracking findings, and managing corrective actions, ensuring ongoing compliance.
- Integration with Other Systems: Integration with ERP, asset management, or CRM systems enhances information flow and supports a holistic approach to quality management.
By aligning maintenance processes with ISO 9001 through the use of maintenance software, organizations can streamline operations, enhance documentation, and strengthen their overall QMS.
Source: fracttal
Bachelor in Industrial Mechanical Engineering
More News About Bachelor InIndustrial Mechanical Engineering