Una implantación TPM comienza con la motivación y preparación del grupo de trabajo. Para ello se habla de tres conceptos japoneses:
- Motivación y concienciación de las personas involucradas en el proyecto.
- Dotar de la habilidad para desarrollar las nuevas tareas que se generarán en el proyecto. Hay que dar formación adecuada a los operarios, personal de mantenimiento, mandos intermedios e incluso dirección.
- Yoruba: entorno de trabajo no hostil.
La formación al operario debe enfocarse en los aspectos siguientes:
- Formación para descubrir anomalías en los equipos. Son los propios operarios los que están a diario con las máquinas y deben ser los primeros en detectar funcionamientos anómalos.
- Formación para tratar estas anomalías. Algunas anomalías menores deben ser tratados inicialmente por los propios operarios.
- Formación para mantener condiciones óptimas de la maquinaria.
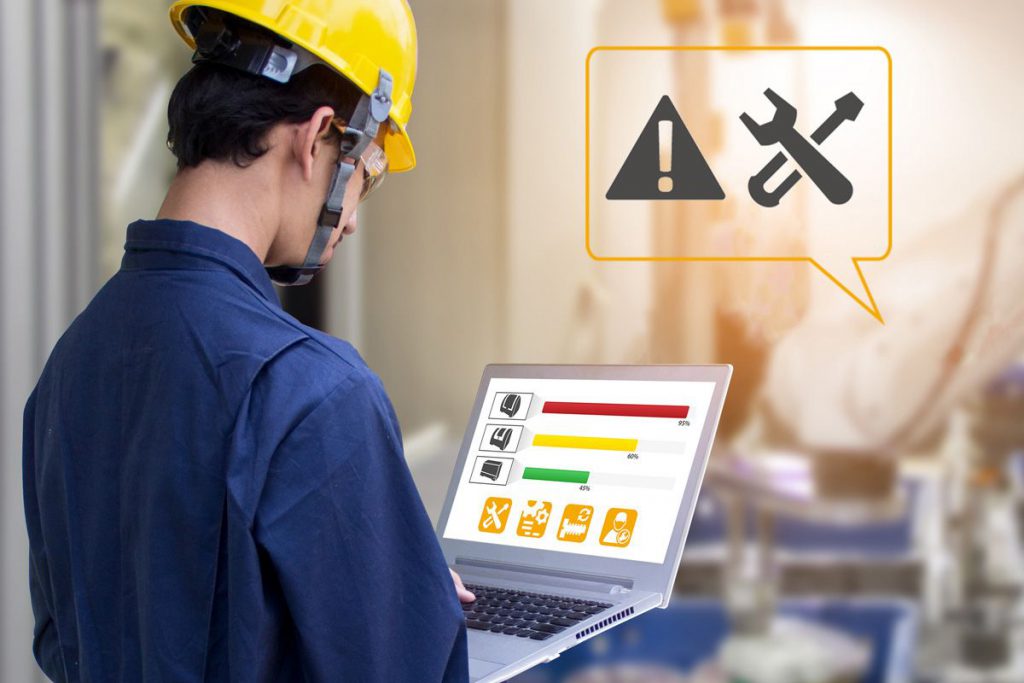
Hay cuatro pasos básicos a seguir en una implementación de TPM.
Fase inicial. Familiarización con los equipos. Hay que hacer un inventario y codificación de equipos, hay que conocer y documentar exactamente lo que se hace a cada equipo.
Al final de la fase deben elaborarse dos documentos: Listado de medios y ficha de cada máquina.
Paso 1. Dejar la línea de producción a un estado lo más parecido posible al estado inicial. Se trata de limpiar y dejar lo mas cercano posible a la situación inicial de cada compra. Así se podrá detectar más fácilmente cambio en las máquinas relativas a posibles fallos.
Para poder realizar este paso hay que dotar adecuadamente a los operarios. Además de limpiar hay que inspeccionar el estado de la línea de anomalías.
Paso 2. Eliminar fuentes de suciedad. Tratar de evitar que la línea se convierta en el mismo estado al que se encontró.
Paso 3. Dar la formación para inspeccionar el equipo. Es importante que el equipo productivo realice tareas básicas de mantenimiento, para tratar que sea lo más autónomo posible.
Paso 4. Introducción de la Mejora Continua con respecto a términos de mantenimiento. Una vez que los equipos productivos ya realizan tareas de mantenimiento, hay que introducir un punto más, la Mejora Continua. Se trata de introducir mejora para el diseño de los equipos con respecto al mantenimiento.
Cada uno de estos pasos deben ser seguidos y gestionados por un grupo de trabajo, y además la finalización de los pasos debe ser validada con una auditoria interna, que verifique que los pasos han sido concluidos realmente.
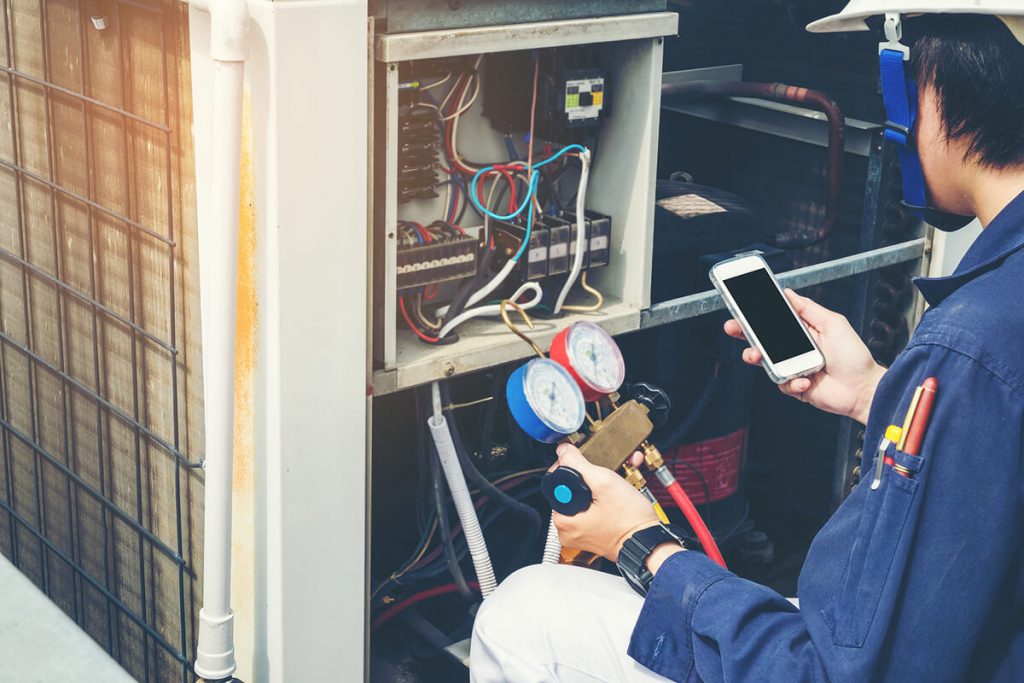
Mantenimiento Productivo Total
CONCLUSIÓN TPM
El TPM (Total Productive Maintenance) o Mantenimiento Productivo Total, son un grupo de herramientas pensadas para realizar mantenimiento preventivo a las máquinas por parte de los empleados, el objetivo es tratar de minimizar los tiempos de parada por averías o fallos de los equipos.
Como primera consecuencia de un proyecto TPM, los operarios deben asumir las primeras tareas del mantenimiento de las máquinas, además de tratar de conservar de forma óptima los equipos.
Los beneficios del Lean TPM son las cero averías, mínimas paradas de la línea, mayor calidad en los productos, y mayor productividad en la producción.
Fuente: Lean Manufacturing
Ingeniería Industrial y de Sistemas de Calidad
Más noticias sobre Ingeniería Industrial y de Sistemas de Calidad…