Predictive maintenance has revolutionized manufacturing, offering a glimpse into the future and empowering businesses to make data-driven decisions that enhance maintenance strategies. No more guesswork—just accurate analysis and forecasting.
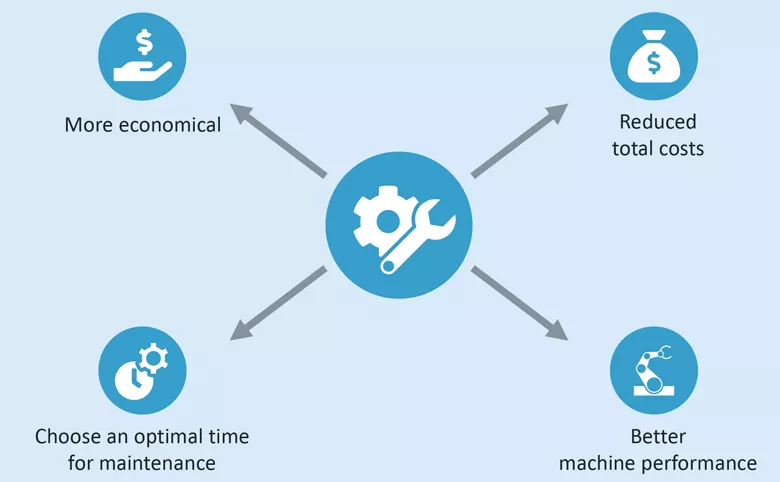
The Benefits of Predictive Maintenance in Manufacturing
Implementing predictive maintenance in your manufacturing operations comes with numerous advantages. Relying solely on corrective maintenance puts your business at risk of unexpected downtime, missed deadlines, and even safety hazards. While corrective maintenance might seem like the easy option—fixing things only when they break—it can lead to costly repairs, legal liabilities, and potentially dangerous situations.
On the other hand, predictive maintenance allows you to preemptively address issues before they escalate. By predicting the optimal time to replace parts or service machinery, you can ensure continuous operation, reduce the risk of unexpected failures, and schedule maintenance during less critical periods. This proactive approach not only keeps your operations running smoothly but also enhances your business’s reputation for reliability and reduces the stress associated with running a manufacturing enterprise.
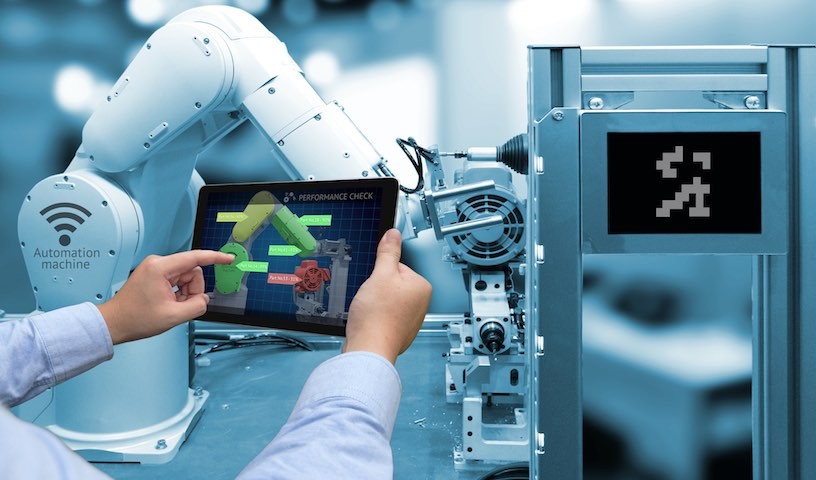
Steps to Implement Predictive Maintenance
1. Leverage Existing Data: Don’t discard your historical data—use it to give your predictive maintenance software a head start. This data, combined with manufacturer information, can significantly enhance the accuracy of your forecasts.
2. Gather Real-Time Data with IoT Devices: Deploy IoT sensors to monitor subtle changes in machinery, such as temperature fluctuations or unusual vibrations. This real-time data helps predict potential failures, allowing your team to intervene before small issues become major problems.
3. Implement Reliable Predictive Maintenance Software: Choose a high-quality software platform like Predictto, which uses advanced AI and machine learning to analyze data and make accurate predictions. Ensure the software is compatible with your existing systems and IoT devices, offering seamless integration and reliable performance.
4. Allow Time for Adjustment: Give your new system time to learn and improve. As it gathers data, the system’s insights and predictions will become increasingly accurate. Train your staff to effectively use the new platform, ensuring they understand its features and benefits. An intuitive, user-friendly system will lead to higher adoption rates and better outcomes.
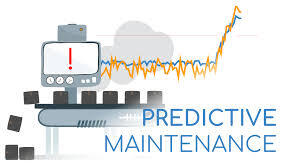
Advantages of Predictive Maintenance Software
Predictive maintenance software, such as Predictto, leverages cutting-edge AI and machine learning technologies to deliver precise maintenance predictions. The more you use it, the smarter it gets, making it an invaluable asset to your business.
By anticipating machine failures and streamlining maintenance schedules, predictive maintenance reduces downtime, enhances safety, and boosts productivity. The investment in such a system quickly pays off, as it saves time, money, and resources in the long run. As the system continues to learn and adapt, its value grows, making early implementation a strategic move.
Predictto integrates historical data, gathers new data from your systems, and works seamlessly with IoT devices. Its intuitive interface provides easy access to comprehensive analysis and insights, enabling you to generate reports, manage maintenance tasks, and receive alerts about potential issues before they escalate.
Predictive maintenance is a game-changer that not only protects your reputation but also drives productivity and profitability. It’s the maintenance strategy of the future, enabling you to foresee potential problems and take proactive measures to keep your operations running smoothly.
Embrace predictive maintenance to secure your business’s future and maintain a competitive edge in the ever-evolving world of manufacturing.
Source: fracttal
Bachelor in Industrial Mechanical Engineering
More News About Bachelor inIndustrial Mechanical Engineering